【5】いよいよ印刷開始
『叙情都市名古屋』 【木村一成写真集】
■2011年11月16日(水) (写真と文:歴遊舎)
本日は、本書の印刷をお願いしている長苗印刷株式会社(本社:名古屋市)の春日井工場で、印刷の刷り出しに、写真家の木村一成とともに立ち会ってきました。いよいよ本番の印刷でございます。
まず、工場長の児島さんから、今回のFM印刷のレクチャーを受ける木村。見本に見せていただいた地図帳をルーペで覗かせていただきます。「う~ん、こ、こ、細かい…」。 いわゆる網点がはっきりする一般的なAM印刷との違いを体感します。
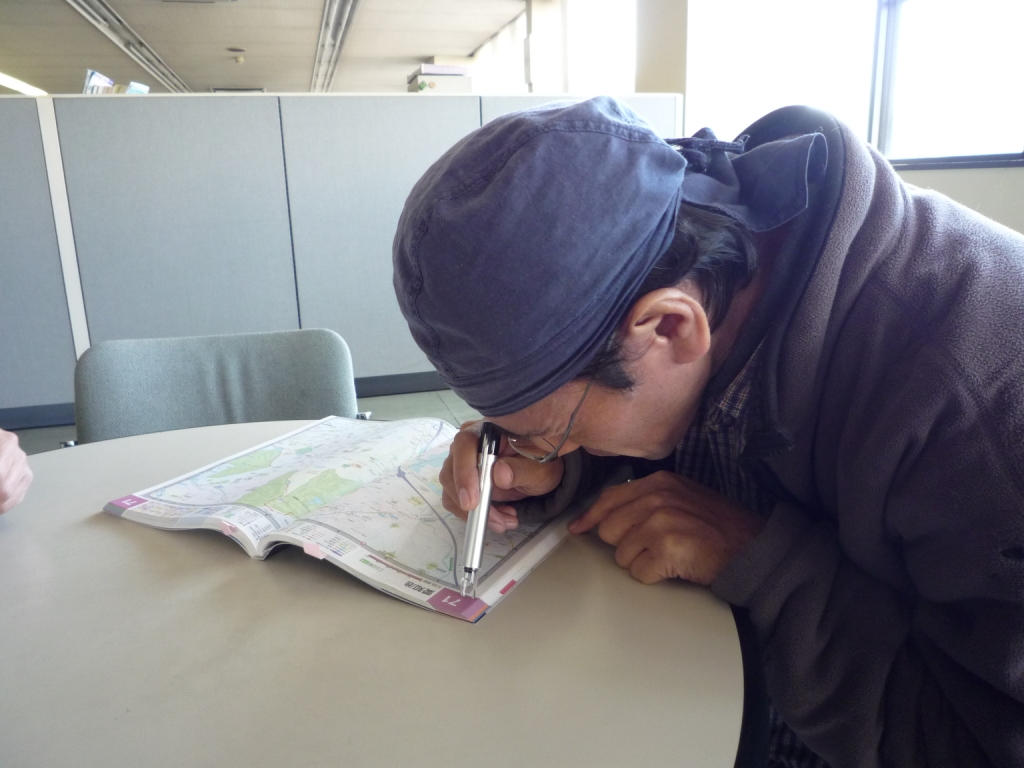
1階の工場へ降りてゆき、そこで生産本部・平版印刷部のチーフマネージャーの河内さんから、さらに突っこんだFM印刷とAM印刷の違いを解説していただきます。
まず、AM印刷で印刷された紙面を、200倍の光学特殊ルーペで覗いた画像をコンピュータ画面上に映し出していただきました。
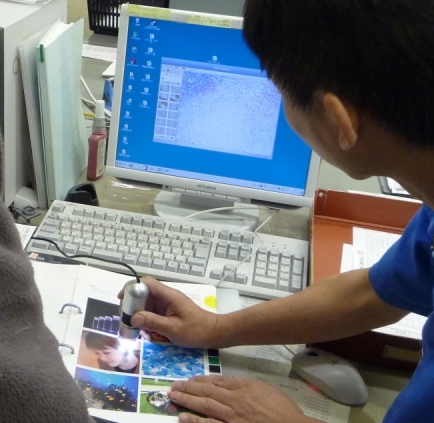
4色分解された網点のドットが、かなり拡大されて見えますね。
次に比較として、FM印刷による印刷物を同じ要領で拡大して見せてもらいますと、「う~ん、こ、こ、細かい…」。木村は2階で見たのと同じ感嘆の声を上げていました。写真では比較しづらいでしょうが、もう、200倍してみると、FM印刷の方が圧倒的にインクのドットが小さく、写真に近い状態で印刷されています。
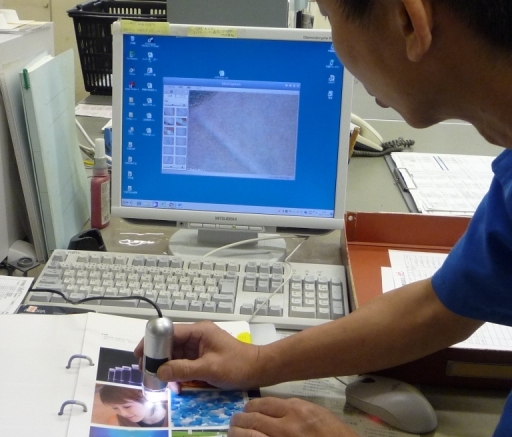
木村も、写真と同じようなイメージで印刷されるこのFM印刷には、高い関心を寄せてきましたが、粒子レベルから見せていただくと、深く納得できたようです。
つづいて、児島さんに工場内を案内していただきますが、「おや? この袋は何ですか?」と木村。児島さんはニコニコしながら、 「片栗粉ですよ」と・・・。
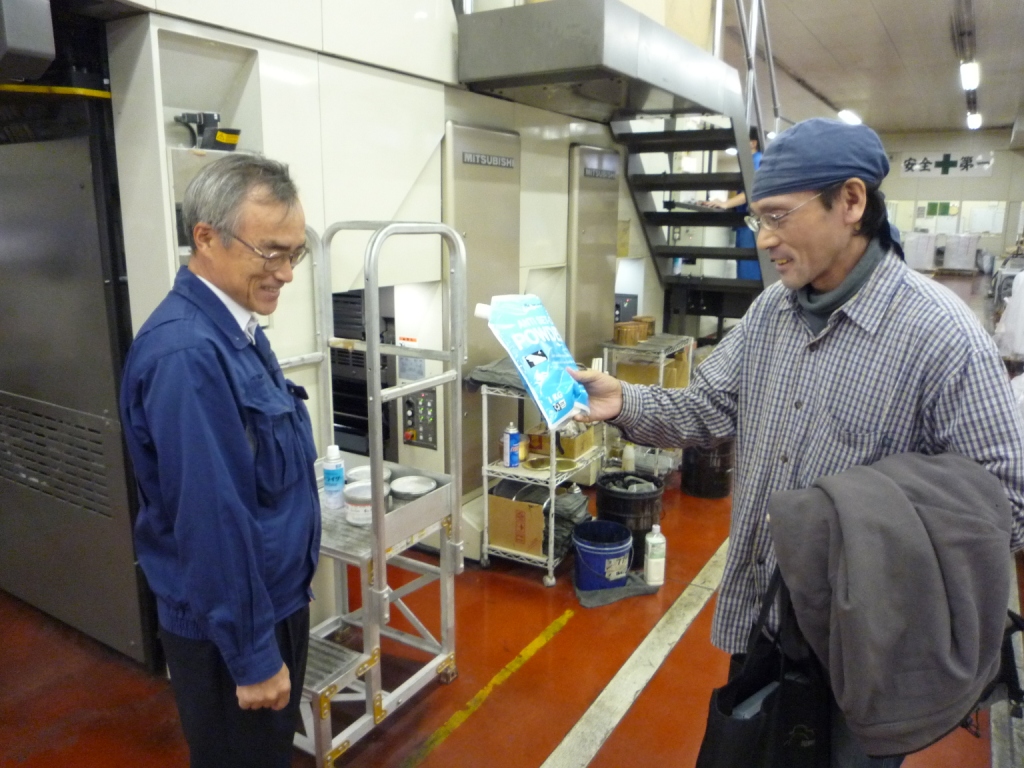
「カ・タ・ク・リ・コ、ですか?」 実は、この粉が、印刷されたばかりの印刷面に薄く撒かれて、下の印刷面とくっつかないようにする役割を果たします。インクは比較的はやく乾くとはいえ、紙に馴染んで落ち着くまでには時間がかかります。「それが、こんな粉でねぇ…」。木村もビックリ。
最近の環境にやさしいインクは、大豆油から製造された天然素材を使っているし、紙の原料のパルプは基本的に樹木だし、これじゃあ、まるで印刷物は植物加工物ですね。美しく仕上がった紙面を見ると、これからは、「おいしい印刷」と言ってしまいそうです。
さて、いよいよ、本日の刷り出しの部門へ。
4色に分解されてできた刷版(さっぱん)が、印刷機に取り付けられたあと、真っ白な原紙が、長い工程を通過して、それぞれの色を重ね、最後の送出口からパン、パン、パンと送り出されてきます。
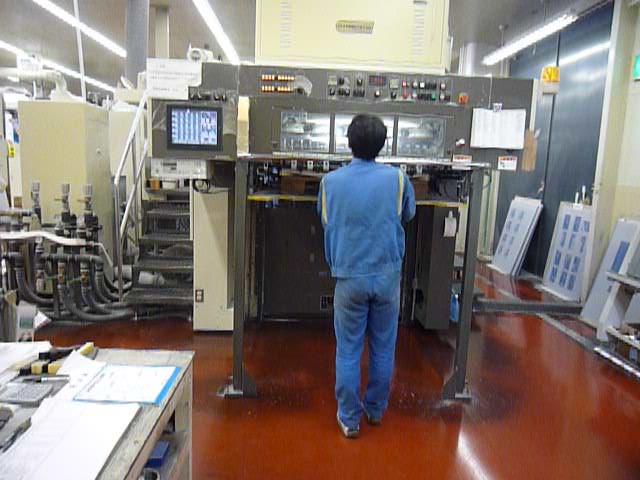
その最後の出口をチェックしてくださっています。ここでは、用紙が波打っておどったり、決められた場所以外に送り出されていないか、時折、真空車といわれるローラーの具合を確かめながら、厳しく監視しています。この送出口にたまる印刷物を取り除いて、下からなかを覗いてみます。
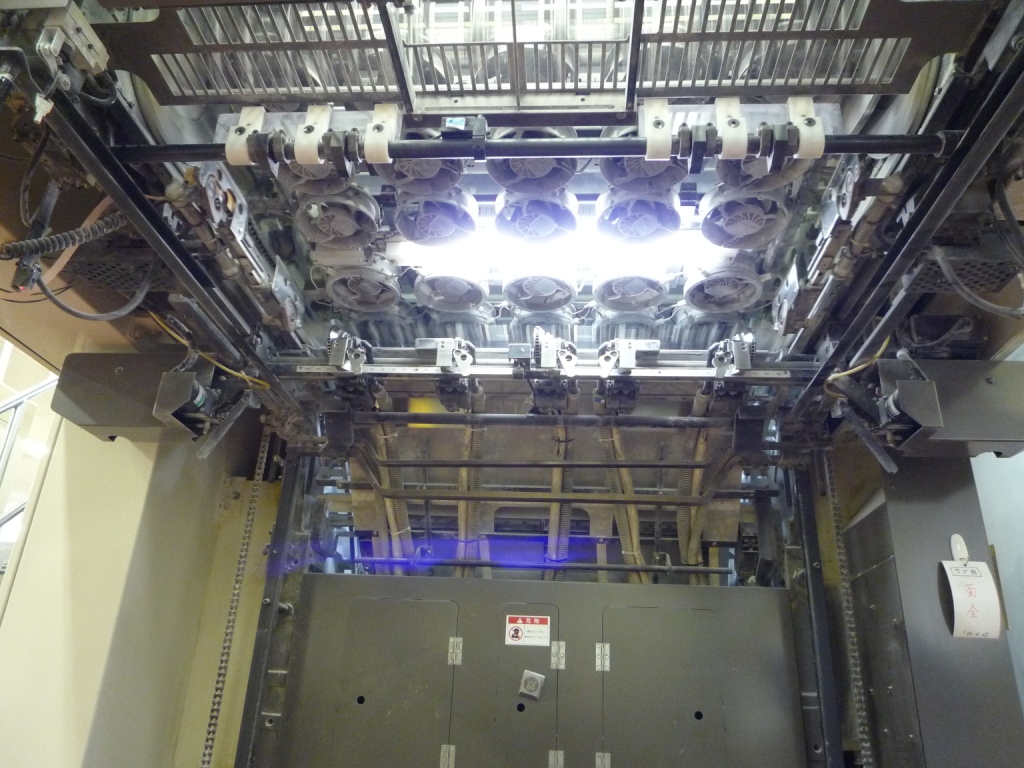
ツメのようなものが付く横棒は、奥から飛んできた紙を下方へ導くガイド。いまその横棒が手前と奥に見えますが、その間に真空車という紙を安定させるブレーキ装置が付いた横棒が、もう一本入ります。真空車は、印刷面をこすらないように、印刷箇所の違いによって、位置をずらせたり、車輪の幅を微妙に変えたりと、結構神経を使うそうです。また、噴射口のような丸い部分は、エアーを吐き出して紙を上から押さえつける装置で、これらのおかげで、印刷された紙は静かに一か所に落ち着くというわけです。
その隣では、次の印刷のために、真っ白な原紙をさばいているところです。
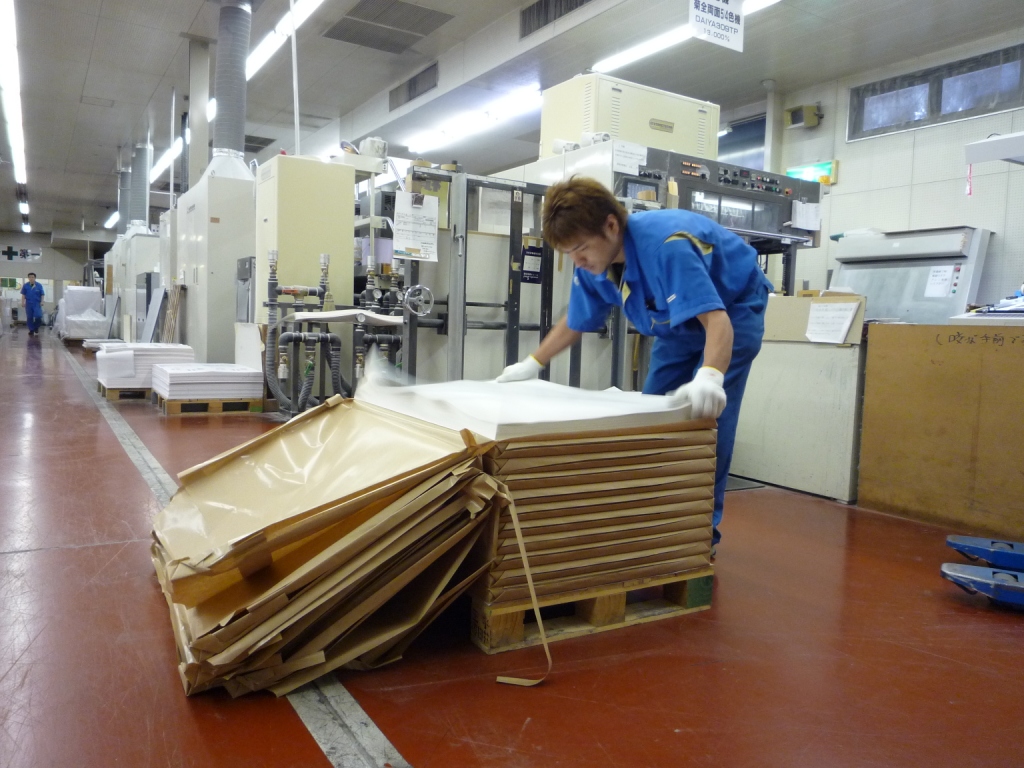
包み紙を開いて束になった用紙を出しますが、これ、かなり重いんです。A全用紙100枚で、しかも写真集用の厚めのマットコート紙なので、ずしりと重い。でも、このまま使うと、紙が重なって出てくる危険もあり、どうするかといいますと、持ち上げて紙の間に空気をいれてバラけさせてやるんです。
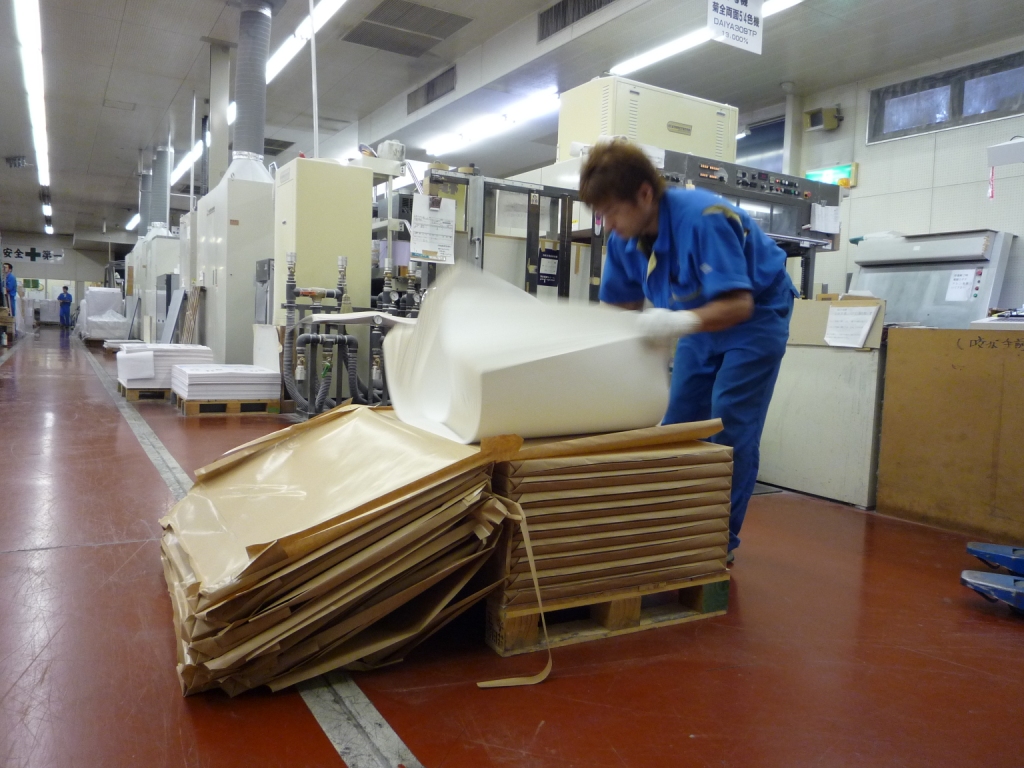
慣れが必要で、そう簡単にはできる技ではございません。わたしたちが、家庭でA4コピー用紙の500枚束に空気を通すのとわけが違います。そして、崩れないように、華麗な手つきで、さっと脇の台に積んでいきます。プロフェショナルの職人さんの動きには、まったく無駄がない。だから華麗なんですね。
さて、刷り上がった紙の印刷状態をチェックしていきますよ~。工場長の児島さんも立ち会っていただき、校正との違いを綿密に検査していきます。
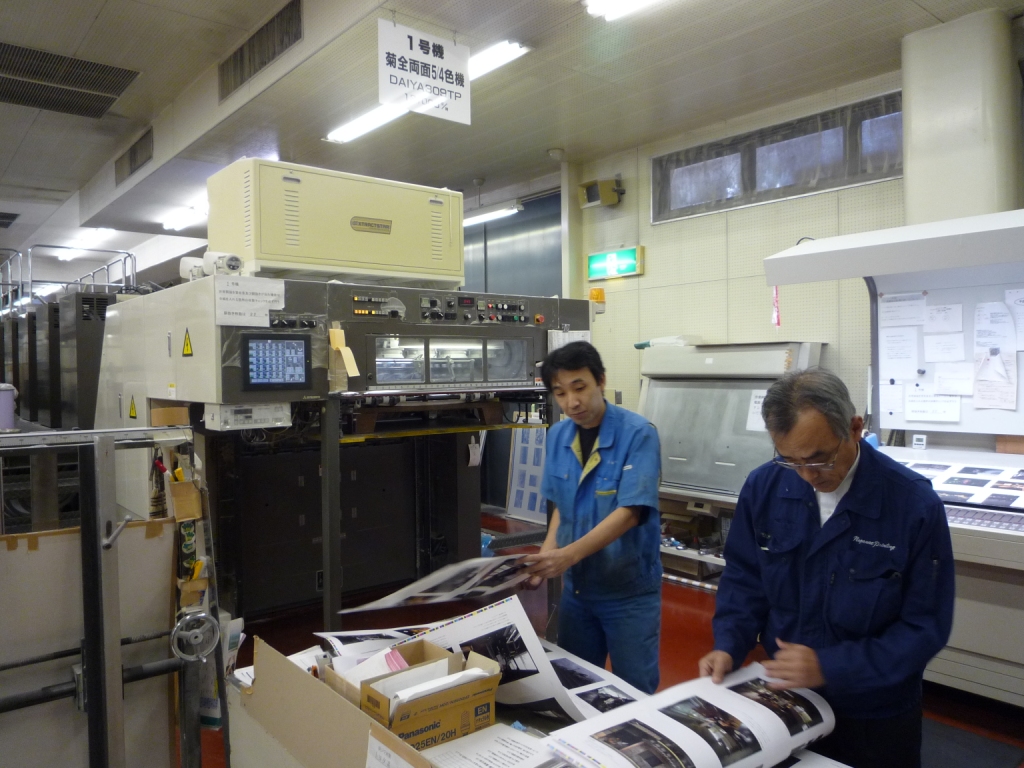
版ズレ、色みのチェックなど、見るべき項目は多岐にわたりますが、印刷紙の端っこに印刷されるカラーチャートの具合を見ただけで、状態の変化はすぐにわかるといいますが、わたしらにはなかなか・・・。そこで、基準光が当たる見台に印刷紙をもっていって、じっくり拝見します。
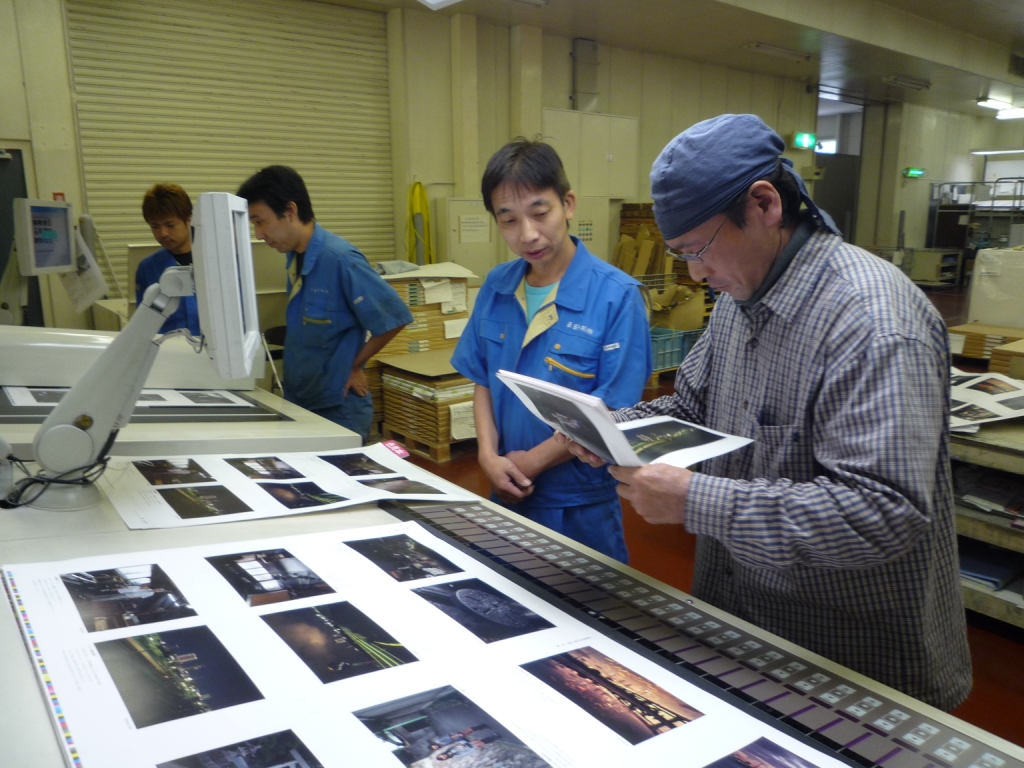
さっそく木村は、持ってきた初校の印刷紙と、再校で調整された、今刷り上がったばかりの印刷紙とを見比べます。河内さんは、丁寧に教えてくれます。
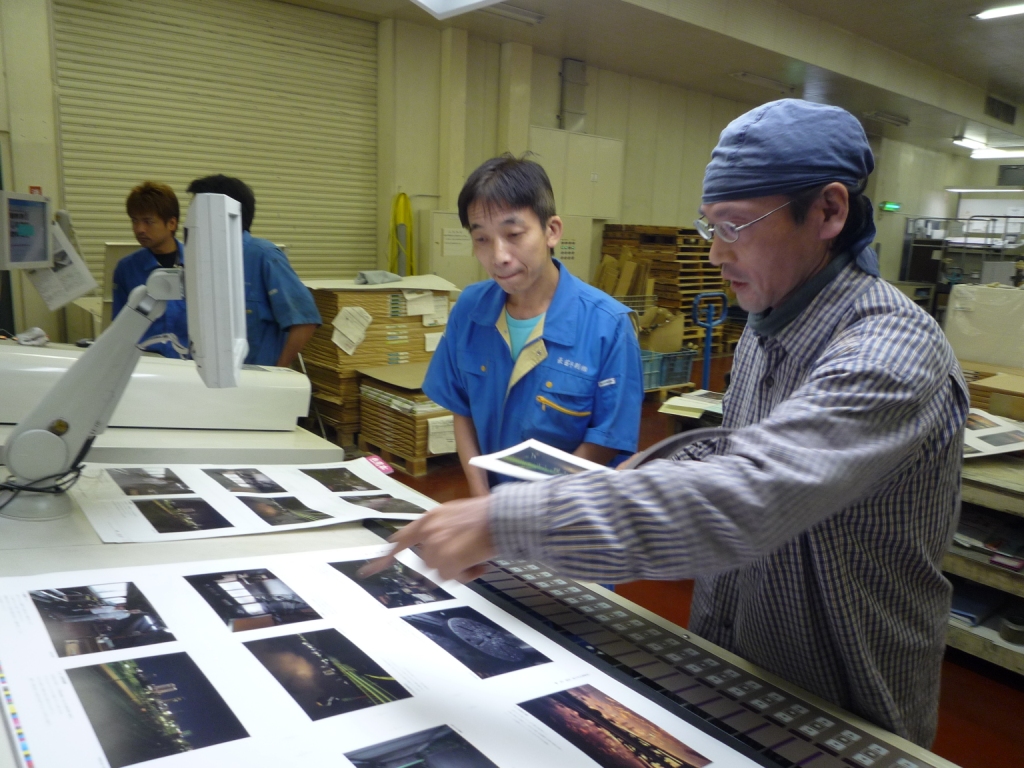
「いや~、ほぼ思い通りといいますか、納得のいく刷りですね~」と、木村も嬉しそうです。写真プリントと印刷されたものが、まったく同じというわけにはいかないことはわかった上で、最高の再現状態を出したいという木村のプロフェショナルな目は、さらに細部への注文を入れます。とくに暗くなった部分の奥に隠れた微妙な色合いを、もう少し立ち上げたい・・・とか。
そこで、さまざまに相談した末に、4色のうち、墨色を若干抑えてみることにしました。隣にある測定器で色みをスキャンして、キャリブレーション(校正)し、前回の基準値から墨のみ1ポイント抜きます。そして、測定器と標準値とを介して、段階的に連鎖する測定の体系を作り上げます。この校正の連鎖をトレーサビリティといいます。
このトレーサビリティをきちんと追っていかないと、何をどうしたのか、あれこれ試行しているうちに、本当に思考が錯誤してしまいますから、大切な記録です。すべてデジタル化してありますので、墨版(黒)へ、1ポイント抑えるインク調節指示を送ります。
それを行なっている間に、河内さんから、基準光の説明を受けます。印刷物は、光によって見え方が違いますから、これが狂わないように、どの光を標準とするかを決めています。それをチェックするのが、これ。
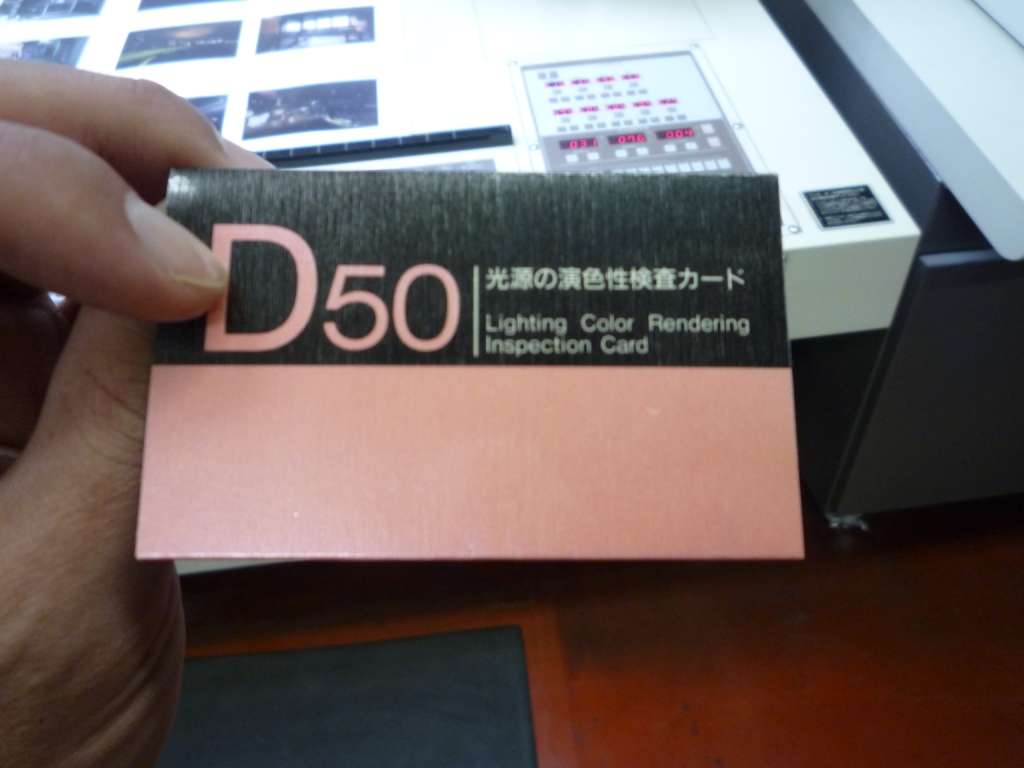
なんでしょ、これ? 実は、2枚の光センサーが貼り付けてあって、その色がピタリと合わないと、基準光ではないことがわかる、そんな道具です。実際に、見台から離れた場所で、このセンサーを開いて見せていただきました。
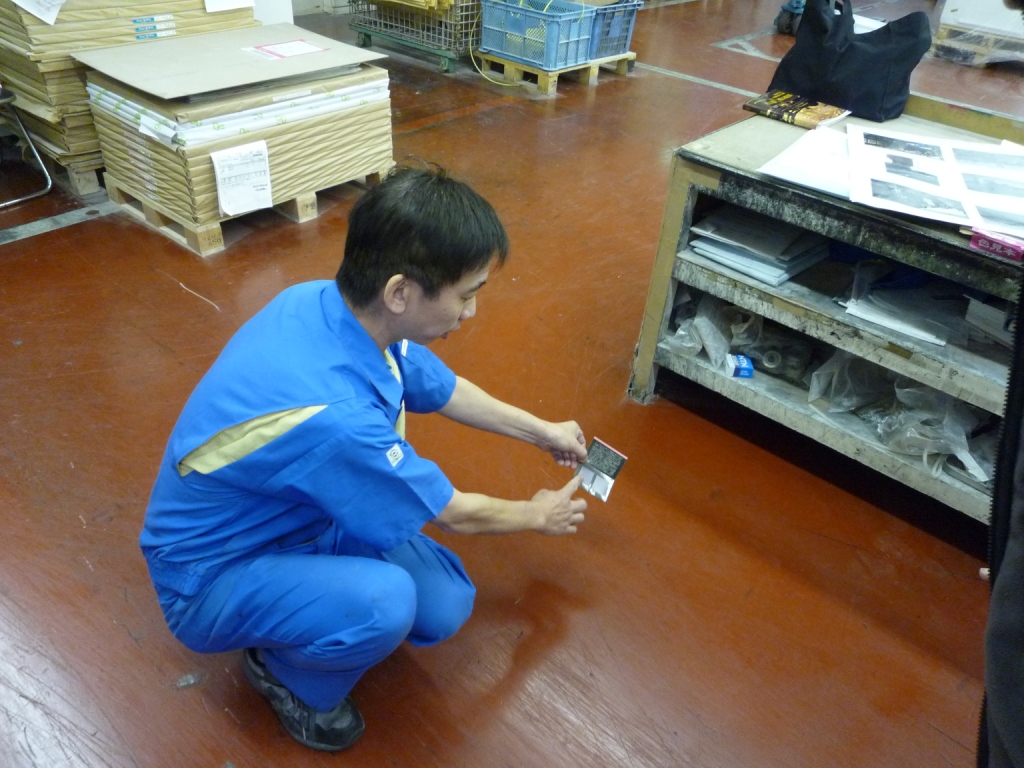
わかりにくいかも知れません。ピンボケだし(汗)。無理やりですが、ちょっと拡大してみますね。
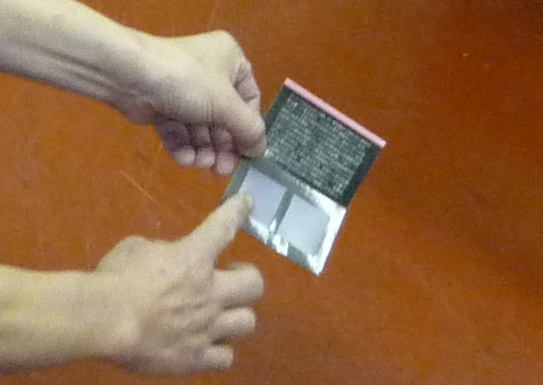
左右で若干ですが、色みが異なりますね。こうなると、基準の光源のある場所へ、印刷物をもっていかなくてはなりません。微妙ですね~、ナイーヴなものなんですね~、光とは…。
次に、印刷機械のメンテナンスについてのお話も伺いました。小さなベアリング。これ、どこに使うのでしょう・・・。
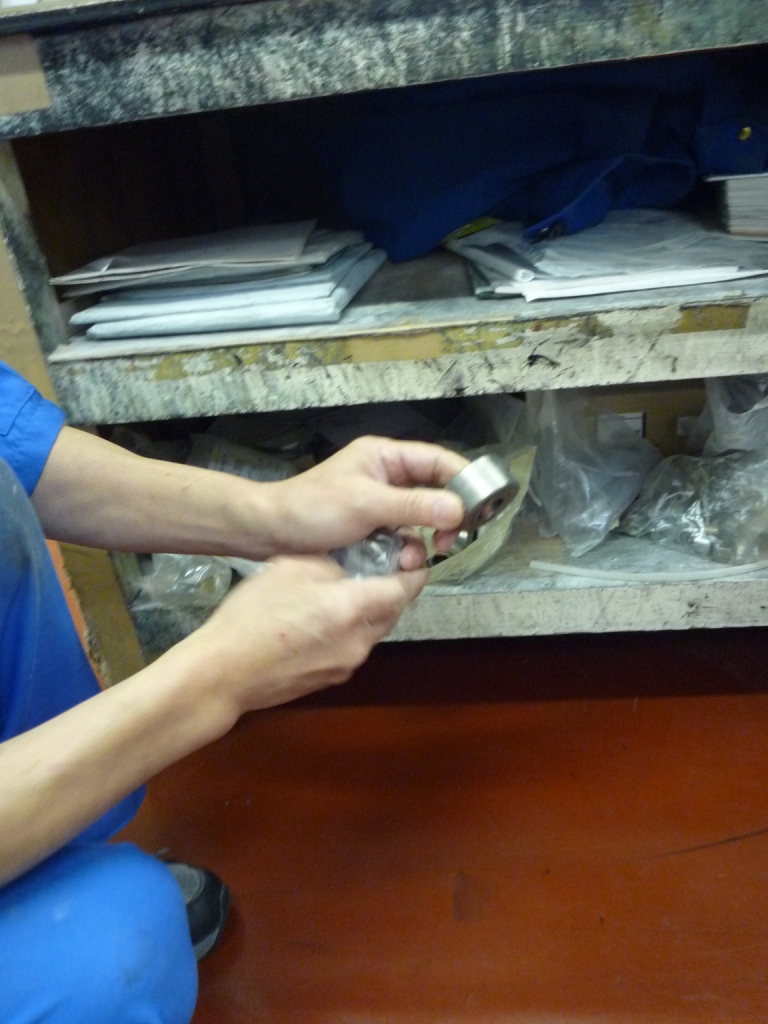
このベアリング、とっても大事な部品なんだそうですよ。カラー印刷機は、前述しましたように、分解された4色のCMYK刷版(シアン/マゼンタ/イエロー/キー・プレート=ブラック)が、通過する白い用紙の決められた位置に確実に印刷されるようにセッティングされています。この超精密なポジションをピタッと決めてくれるのが、ツメ軸トーションバーという部分で、この軸をガタが出ないように滑らかに動かす役割を担うのが、こんな小さなベアリングなんです。
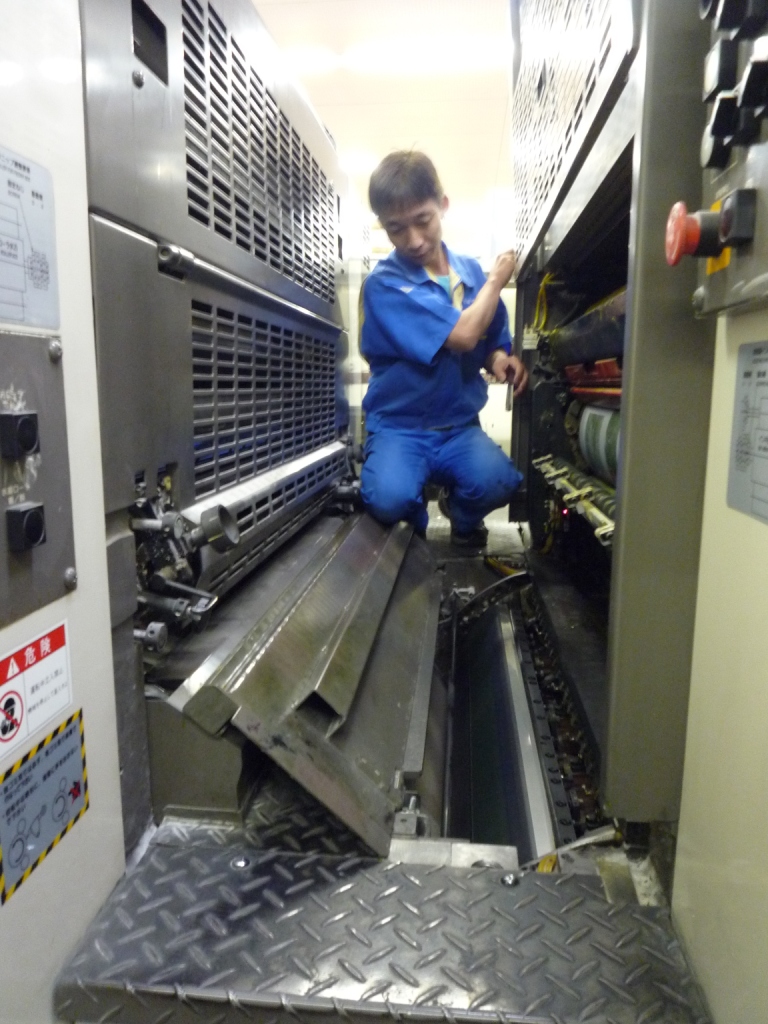
実際に、その機械部分を開けて見せていただきました。なかなかここは、見られませんよ。ここが減ってガタが出るようでは、版ズレも起こしかねませんから、まだ十分に使えるという時期でも、早め早めに交換して、安定した品質を保証しなければなりません、と河内さんは力説します。
日本の印刷技術は、機械技術の発達に支えられながらも、こうしたマメなメンテナンスもあいまって、世界最高クラスを誇っています。部品ひとつひとつも、耐久性や高い精度の品質をもち、まことに美しい印刷をわたしたちは日常生活で目にすることができるのです。
そして、何よりも、細かいミスも逃さない徹底した工程管理とチェック技術、そして過去のデータの膨大な蓄積からフィードバックされる、どんな難しい客注でもこなしてしまう職人技。しかし、最後の最後は、機械ではなく、この人間の経験と勘という部分が、「ものづくり日本」の恐るべき技術力を強固にしているのです。
いよいよ、最後の印刷になりました。表紙の印刷に入っていきます。少し濃いめの感じの方が、色が紙に馴染んで落ち着いて薄くなったあと、ちょうどよくなる…という指示が出ます。
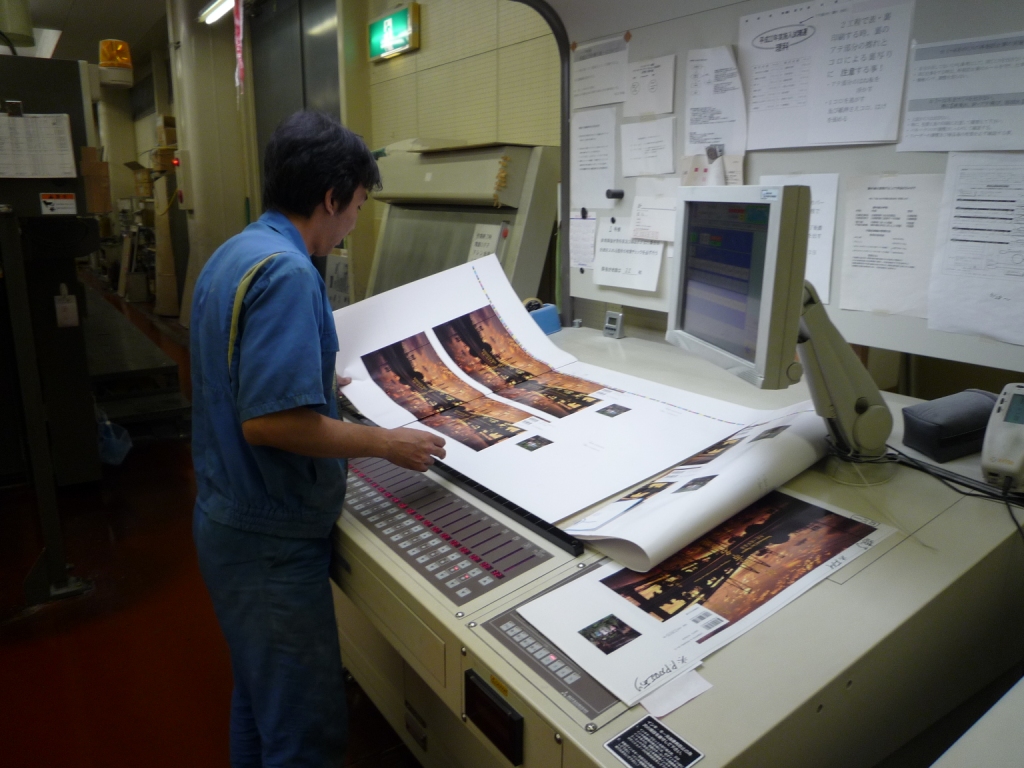
今回の表紙では、最後にPPという光沢コーティングを施すために、そこでまた若干色が深く見えてきますから、本の表紙という、もっともインパクトを必要とする部分における、写真表現の魅力を最大限に引き出すために、最適の色を作っていただけました。これが、職人技というものでしょう。
刷り上がった印刷紙は、印刷面が紙に馴染むまで、最低でも4時間~5時間は寝かしておかねばなりません。
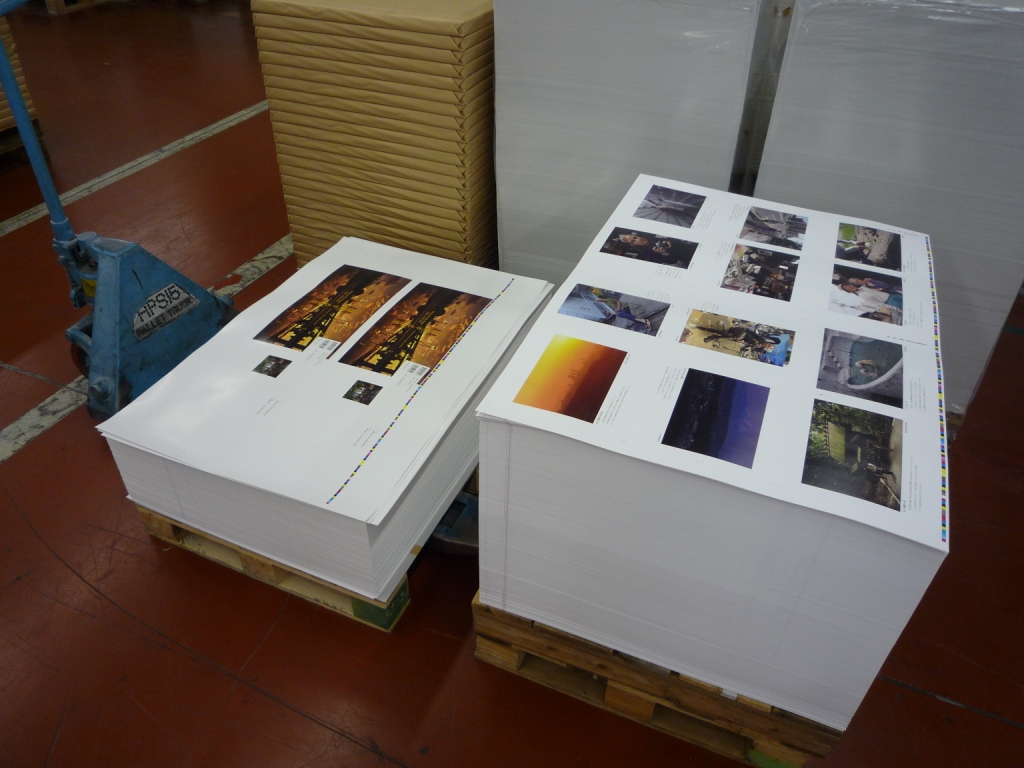
こうして、刷り上がった印刷紙は、静かに熟成を待つのです。そして、製本会社にまわって、余分な部分を裁断され、1丁2丁と8ページ1セットに折りたたまれて、本として背中を綴じて製本されていくのです。
みなさんのお手元には、こうした数々の工程と職人技による厳しいチェックを通過した「入魂の書籍」が、届けられるものと思います。
新刊の書籍を手に取ったとき、なんだか写真表面にサラサラした粉っぽいものがついていたら、こんな印刷の過程を思い出して、末長く大事にしてやってください。
長苗印刷さん、素敵な印刷をありがとうございました。その真心は、きっと読者に伝わると信じています。
■『叙情都市名古屋』のご注文は→こちら